From August 14 to 17, 2024, the Chinese Society for Metals (CSM) held the 2024 National Metallurgical Energy and Environmental Protection Production Tech Conference and High-End Forum on Green Low-Carbon Metallurgy in Baotou. Focusing on “Scientific Pollution Reduction, Energy Saving, Carbon Reduction, and Efficient Synergy for Green Development”, the conference emphasized the exchange and discussion of technologies, processes, and equipment related to green low-carbon development, cost reduction, oxygen-enriched combustion, desulfurization, carbon capture and utilization, pollution reduction, and environmental protection cost reduction. PKU Pioneer closely follows the green development of the steel industry, and presented a technical report titled “Industrial Exploration of Low-Cost Blast Furnace Oxygen Enrichment, Steel-Mill Gas Purification and High-Value Utilization” at the conference as a high-quality supplier of gas separation technology in the steel industry.
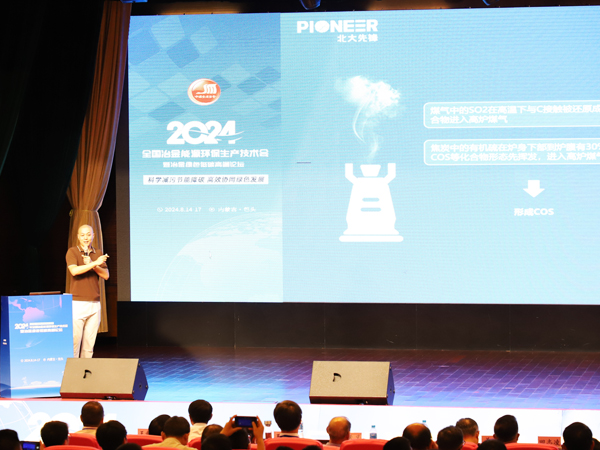
Zhang Yi, the Director of Environmental Production Business at PKU Pioneer Delivering the Technical Report
Currently, the steel market is facing significant supply-demand imbalances, with steel prices remaining low. Some product categories are experiencing intense internal competition, leading to a year-on-year decline in industry profits and drops in output, price, and profit. Under these new circumstances, steel mills are focusing on energy-saving, efficiency improvement, and cost reduction, as well as the urgent need to explore ways to reduce production and environmental operation costs while meeting international standard requirements. Zhang Yi, the Director of Environmental Production Business at PKU Pioneer, presented energy-saving, emission-reduction, and carbon-reduction solutions during his technical report.
1. Energy Saving: Blast Furnace Oxygen Enrichment
In the past 20 years, China's VPSA (Vacuum Pressure Swing Adsorption) oxygen generation technology has seen rapid development, making it the most widely applied country in the world. Twenty years ago, VPSA technology could only generate an oxygen flow of 1,000Nm³/h. With continuous technological iterations, PKU Pioneer’s VPSA oxygen units can now stably meet oxygen demands as high as 80,000~100,000Nm³/h, which have already been in mature use at multiple steel companies.
Besides oxygen enrichment of blast furnaces, the upgrading of oxygen-enriched and oxy-fuel combustion in steel rolling reheating furnaces has also been a hot topic in the industry in recent years. VPSA oxygen generation technology is suitable for reheating furnaces, especially in production conditions where oxygen purity requirements are not high, turndown ratio demands are significant, and low-cost oxygen supply is needed.
Compared with traditional cryogenic air separation oxygen generation equipment, VPSA oxygen generation significantly reduces energy consumption, overall investment, and operation & maintenance costs, providing support for steel companies in achieving economical oxygen supply, production capacity expansion, energy conservation, and efficiency improvement.
2. Emission Reduction: Steel Production Gas Fine Desulfurization
With ultra-low emission retrofitting in steel enterprises has become a widely discussed topic, the fine desulfurization of blast furnace gas (BFG) and coke oven gas (COG) is a policy requirement to control SO₂ at the source. Taking the example of PKU Pioneer constructing a fine desulfurization system for two 1200m³ blast furnaces at Baotou Steel Wanten in 2022, with a total blast furnace gas volume of 600,000Nm³/h, the sulfur content at the inlet of the fine desulfurization system was monitored in real-time, with COS around 120mg/Nm³ and H2S around 20mg/Nm³. After treatment by PKU Pioneer’s desulfurization system, the total sulfur content at the outlet was less than 20mg/Nm³ and remained stable <10mg/Nm³ for extended periods. The fine desulfurization system's process is characterized by high desulfurization precision, with the high-efficiency desulfurizing agent independently developed by PKU Pioneer achieving a long service life of 8-11 months.
3. Carbon Reduction: Co-Production of Steel and Chemicals
The by-product gases from the steel production process mainly include BFG, BOFG and COG, collectively referred to as steel-mill gases. The effective components of these gases are CO, H2, and CH4, which are primarily combusted for power generation now. The core of low-carbon utilization is to leverage the chemical and reduction properties of steel-making gases while minimizing their use as fuel. Presently, China’s successful cases of low-carbon utilization of steel-making gases primarily involve their chemical properties, known as co-production of steel and chemicals in the steel industry.
Shiheng Special Steel's refined management is widely recognized in China steel industry. During the economic downturn when the whole industry is generally experiencing widespread profit declines or losses, Shiheng Special Steel has managed to maintain a profit of over $28 per ton of steel. In 2018, Shiheng Special Steel's steel and chemicals co-production line was officially put into operation, which converts BOFG, as the feedstock, into the production material for 200,000 tons of formic acid annually through PKU Pioneer’s steel-mill gas utilization technology. The formic acid product is of high quality and profitability, and carbon emissions of 320,000 tons per year were reduced at the same time. The project has become a typical demonstration of steel and chemicals co-production and has attracted many steel companies to visit for benchmarking exchanges.
Steel and chemicals co-production, as a new model for the coupled development and circular economy for steel enterprises, opens up new business areas and investment channels for steel mills. With significant carbon reduction effects, it helps to not only achieve ultra-low emissions but also further control SO2, NOx, and dust emissions. Steel and chemicals co-production is a novel model for integrating resource utilization, reducing primary energy consumption, and decreasing pollution emissions as a feasible approach for cross-industry coupling, green development, and circular economy benefits.
Experts believe that China's steel industry should focus on green fuels, and simultaneously work on the source, process, and end industries to achieve "3 transformations." At the source, use clean energy and upgrade raw materials to adopt more green fuels. During the process, optimize furnace structure and the production processes, including manufacturing new types of furnaces, adopting short electric furnace steelmaking and new processes like electrolytic ironmaking. At the end, strengthen the treatment and utilization of secondary solid waste by desulfurization and denitrification.
Therefore, improving the quality and efficiency of upstream oxygen-enriched blast furnace ironmaking, implementing front-end fine desulfurization of blast furnace gas in the midstream, or purifying downstream steel plant gases to achieve steel and chemicals co-production, are all feasible paths for steel enterprises to explore effectively under the dual carbon goals.
As a leading VPSA/PSA gas separation solutions provider worldwide, PKU Pioneer has served over 80 top iron and steel mills. By offering VPSA/PSA oxygen generation plants, we successfully helped the users achieve cost-effective industrial oxygen supply for blast furnaces and electric arc furnaces. Also, many steel makers adopted PKU Pioneer’s PSA-CO and H2 plants to purify high-purity CO (95-99.9%) and H2 gas (up to 99.999%) from steel-mill gases for the synthesis of various chemical products like ethylene glycol, formic acid, acetic acid, acetic anhydride, butanol, 1-octanol, polycarbonate, toluene diisocyanate (TDI), dimethyl formamide (DMF), and dimethyl carbonate (DMC). Through rich engineering experience and continuous innovations, PKU Pioneer will continue to make our contributions to the green and sustainable development of the world steel industry.