On August 14, 2024, supported by PKU Pioneer, a conference on the Technical Requirements for VPSA Oxygen Generation for Blast Furnace Ironmaking Standard and Energy-Saving Environmental Technologies was held by the Chinese Society for Metals (hereinafter referred to as CSM) and in Baotou. The conference was chaired by Professor Li Jingshe, Deputy Secretary-General of the Special Steel Branch of CSM and a professor at the University of Science and Technology Beijing. Experts including Wang Tianyi, Chairman of the Expert Committee of CSM, Hao Zhizhong, Deputy Secretary-General and Wang Yinsheng, Deputy Director of the Production Technology and Publications Department, attended the meeting along with expert teams from over 20 steel companies such as Baosteel, Shougang Group, Tangsteel Group, Shandong Steel, Qian'an Iron & Steel, Xinjiang Ba Yi Iron and Steel, Ansteel Group, Meishan Iron and Steel, Wusteel, Hunan Valin Xiangtan Iron and Steel, Hunan Valin Lianyuan Iron & Steel, Jiangsu Yonggang Group, Zenith Steel Group Company Limited, and Hebei Tangyin Iron and Steel, etc. They engaged in discussions on topics such as oxygen-enriched combustion in the steel industry, cost reduction and efficiency enhancement, pollution reduction, energy saving, and lowering environmental operating costs. The experts shared production experiences and energy-saving measures as well as new technologies and achievements to promote ultra-low emission control and green, low-carbon development in the steel industry.
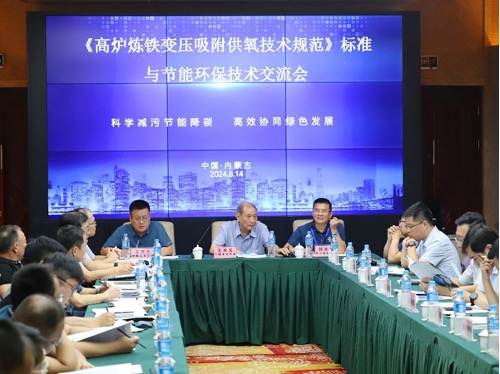
Conference on VPSA Oxygen Supply Standard and Energy-Saving Technologies for Blast Furnace Ironmaking
At the meeting, Wang Yinsheng introduced the market application background of the group standard Technical Requirements for VPSA Oxygen Generation for Blast Furnace Ironmaking, which was drafted by PKU Pioneer and implemented in December 2022. This is China's first technical standard for oxygen supply in blast furnaces using VPSA (vacuum pressure swing adsorption) in the steel industry. He mentioned that not only blast furnaces but also heating furnaces and other heating operations require oxygen, and industrialized oxy-fuel combustion technology for heating furnaces is available in China currently. CSM will also focus on promoting these new technologies and equipment to steel mills to benefit more steelmakers as obtaining more cost-effective oxygen is crucial for technological advancement in the future.
Subsequently, Lei Zhigao, Deputy Director of the Energy Plant at Hunan Valin Lianyuan Iron & Steel (LY Steel), shared solutions for addressing oxygen shortage. In 2019, due to strong market demand driven by stable development of downstream industries such as infrastructure and real estate, LY Steel’s molten iron production was insufficient to meet the needs of subsequent steelmaking and rolling processes. To increase the output, the oxygen enrichment rate in the blast furnace was raised from 3% to 10%, leading to an increase in the oxygen demand. Large-scale liquid oxygen procurement even caused liquid oxygen prices to fluctuate sharply, with costs rising from $84/t to $168/t. Considering the long construction time for cryogenic oxygen production equipment, they decided to install multiple VPSA oxygen generation units, designed and built by PKU Pioneer, to supplement oxygen production capacity in the short term.
The total investment in this quality improvement and optimization project reached $41,985,900. The VPSA oxygen equipment has generated 1.495 billion Nm3/h of oxygen since
its operation, saving $47,863,926 in oxygen costs while the overall economic benefits of the project have already exceeded the oxygen plant investment. Moving forward, LY Steel plans to promote oxy-fuel and oxygen enrichment technology in boilers, heating furnaces and sintering furnaces to further expand the application of energy-saving technologies and enhance its competitiveness.
In terms of ultra-low emissions control for air pollution, Cui Shengli, Director of the Ironmaking Plant at Hebei Tangyin Iron and Steel, shared his experience with fine desulfurization. He mentioned that fine desulfurization of blast furnace gas (BFG) is a relatively advanced technology. Using front-side dry fine desulfurization technology, the SO2 content in the 800,000Nm3/h BFG was detected to be only 2-3 mg/m³ after the desulfurization equipment was put into operation. Despite the complex blast furnace operating conditions where fluctuations in BFG temperature and impurity contents pose challenges to the stability of the desulfurization equipment, the hydrolysis and desulfurization agent in the system is able to be used for more than 12 months, with some lasting up to 14 months, and the hydrolysis efficiency reaches 99% when the hydrolysis tower temperature is controlled between 70-75°C. Domestically, it is rare for fine desulfurization equipment's hydrolysis and desulfurization agents to last over 12 months, and PKU Pioneer is one of the few technical service providers capable of achieving this.
Dr. Guo Yuhua, a technical expert from Shandong Steel Chemistry Technology Co., Ltd., highlighted the importance of integrated steel and chemical production in carbon reduction for the steel industry. He noted that besides supplying heating furnaces, surplus gases from steel plants is typically used for power generation. As technology advances, the surplus gases amount is expected to increase due to the fact that renewable energy generation capacity has surpassed traditional power generation since 2024, with wind and solar power exceeding hydropower. As a result, thermal power generation may face further restrictions. For steel manufacturers, BFG can be carbonylated to produce methanol, and coke oven gas (COG) can be used to synthesize various chemical products. Steel companies in Shandong are considering purifying H2 from COG and CO from converter gas to synthesize ethanol, showing significant potential for steel-chemical co-production.
In 2018, PKU Pioneer established the world's first CO purification project from converter gas to produce formic acid at Shiheng Special Steel Group Co., Ltd. In the same year, PKU Pioneer signed a contract for a second steel-chemical co-production project with Shanxi Liheng Steel Group to purify CO from converter gas and H2 from coke oven gas, which were then used as feedstock for synthesizing ethylene glycol, thereby extending the steelmaking process into the chemical industry.
CSM organized this technical exchange conference to help steel enterprises gain a deeper understanding of national policy directions. In May 2024, the National Development and Reform Commission, the Ministry of Industry and Information Technology, the Ministry of Ecology and Environment, the State Administration for Market Regulation, and the National Energy Administration jointly issued the “Special Action Plan for Energy Conservation and Carbon Reduction in the Steel Industry”, which states that from 2024 to 2025, energy-saving measures and equipment upgrades in the steel industry will result in energy savings of approximately 20 million tons of standard coal and a reduction of about 53 million tons of CO2 emissions. By the end of 2030, the energy efficiency of key processes in the steel industry should be further improved, with that of major energy-consuming equipment reaching advanced levels. The comprehensive energy consumption and carbon emissions per ton of steel should be significantly reduced while the energy usage structure should be continuously optimized, and advanced energy-saving and carbon-reduction technologies, such as oxygen-enriched blast furnace technology and hydrogen metallurgy, will achieve breakthroughs to lead to significant progress in the industry's green, low-carbon, and high-quality development.
It can be seen that by the end of 2025, China's steel industry will focus on the energy conservation and carbon reduction goals outlined in the special action plan. The industry will work towards optimizing industrial structure, implementing energy-saving and carbon reduction transformations, updating energy- consumption equipment, promoting green and low-carbon energy usage, recycling energy resources, and advancing digital upgrades. PKU Pioneer will offer leading gas separation & purification technologies and solutions to help steel mills achieve innovative technology applications and low-carbon environmental improvements to accelerate new breakthroughs.
Based on advanced VPSA/PSA oxygen generation technology, PKU Pioneer has successfully set up over 300 oxygen units, with a total oxygen production capacity of 2,000,000Nm3/h, to worldwide enterprises to provide a reliable and cost-effective oxygen source. By offering quality oxygen, CO and H2 solutions to over 70 steel mills, PKU Pioneer not only supports steel mills in enhancing blast furnace ironmaking and EAF steelmaking efficiency but also contributes to their goals of achieving green and high-quality development.